The Infrastructure That Powers Omni PGA Frisco
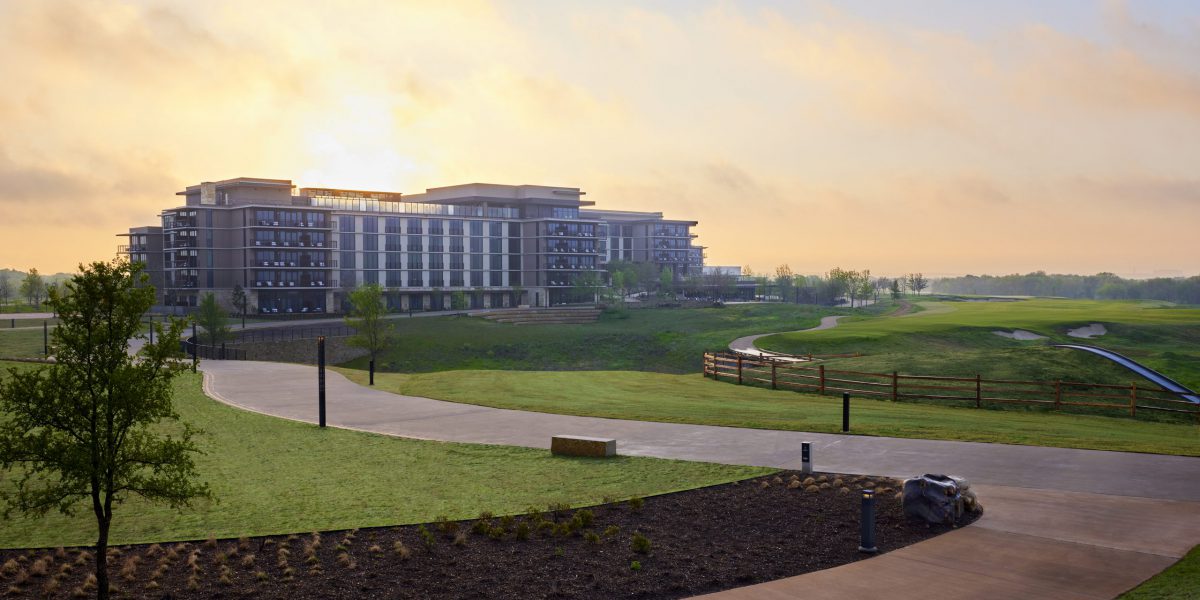
Golf’s Most Highly Anticipated Resort
Six hundred sixty acres on the northernmost fringe of bustling Frisco, Texas, a suburb of Dallas, were meticulously draped in half a billion dollars’ worth of lavishly exquisite luxury that has taken shape as the Omni Frisco PGA Resort. Golf’s most highly anticipated resort in the Western Hemisphere consists of a 500-room hotel with 127,000 square feet of indoor and outdoor event space, including a free-standing event pavilion, 13 dining options, a massive two-story 15,000 square foot full-service spa, a PGA performance center, a retail village that contains multiple dining and entertainment options including a Lounge by Topgolf, and ten free-standing villas serviced by the hotel.
As one may have ascertained from the “PGA” portion of the project’s title, the latest addition to Omni Hotels & Resorts’ iconic portfolio will play host to some of pro golf’s most popular events and star-studded athletes. Omni PGA Frisco also hosts the largest natural grass putting and chipping green in the United States, supplemented with over two acres’ worth of lighting courtesy of Alvine. “The Swing,” a 10-hole executive course that can be enjoyed after dark, is also available thanks to Alvine-powered exterior lighting systems.
Alvine was responsible for providing the mechanical, electrical, plumbing (MEP), and fire protection design services for the expansive hotel, clubhouse, retail village, event center, maintenance facilities, support buildings, villas, and exterior power distribution for the executive course and the putting greens, and the golf course irrigation pump house. Providing services for a slated-to-be world-renowned resort is no easy feat. Fortunately, Justin Olson, P.E., provided extensive design work, bringing the facilities to life with intelligently-construed, durable electrical infrastructure. Tjaden Ahrens, P.E., was equally instrumental in adjusting the designs and procedures for the project’s mechanical components during the construction administration phase.
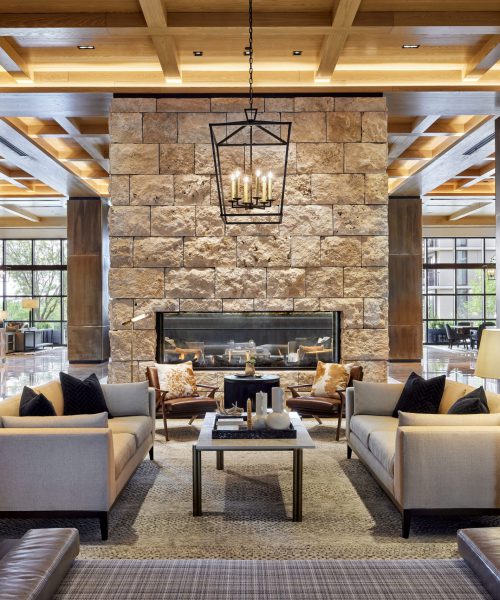
A Texas-sized Resort
The old adage is true: Everything is bigger in Texas, from the show-stopping design of the resort’s interiors to the infrastructure it takes for their facilities to perform.
The project had seven separate standalone drawing packages: hotel, clubhouse, villas (Alvine was only involved with the villas through the schematic design phase), retail village, PGA performance center, golf support buildings, and food bunker. The number of drawing packages complicated the design delivery, but they were necessary for the project to meet the construction schedule. Alvine issued the golf course support building package months before the other facilities. The pump house needed to operate for two years before opening the course to irrigate the bermudagrass fairways, roughs, and putting surfaces. All other design packages were staggered.
The estimated demand for the entire campus, as allowed by the National Electric Code, was 14 megawatts (14,000,000 watts).
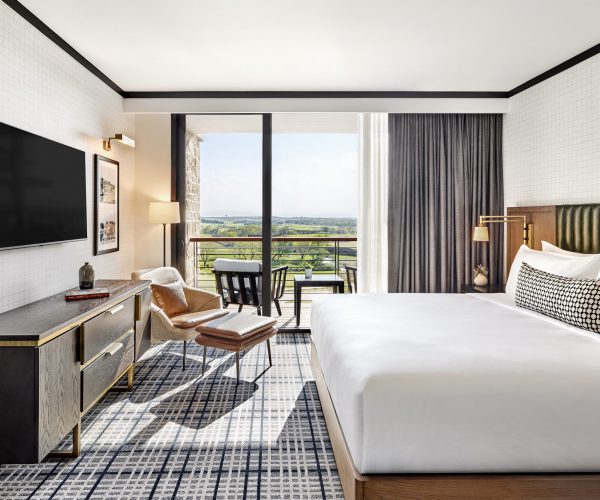
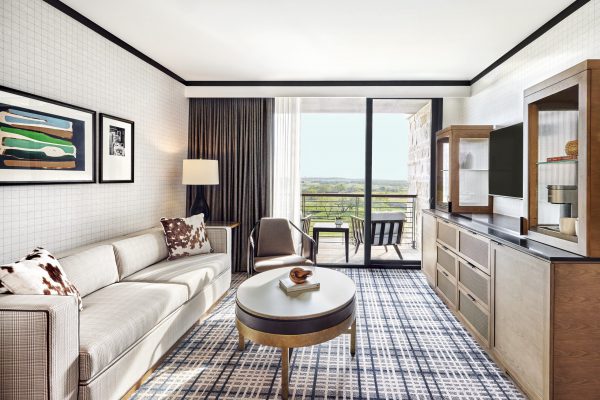
On Solid Ground?
While the majority of hotel projects that MEP engineers work on of this size and scale are vertically constructed, with mechanical equipment below and cooling towers above the structure, the Omni PGA Frisco resort’s principle design was the inverse. The project had a much larger horizontal footprint and was purposefully kept below the Frisco-amended high-rise definition of 55 feet.
This central plant contains three water-cooled centrifugal chillers with three 940-gallon-per-minute (GPM) chilled-water pumps. The resort placed three 550-ton cooling towers on the roof of the mechanical plant. The cooling tower system has three 1,500 GPM condenser water pumps. Each tower fan and pump are equipped with a variable frequency drive offering the site reduced peak energy demand and beneficial energy savings. One cooling tower and one pump satisfy a minimum of 50% of the chiller’s heat rejection load. The cooling towers have a chemical treatment system to minimize scale, microbiological growth, and corrosion which offers the resort’s mechanical equipment more longevity, ease of maintenance, and significantly lowers the facility’s maintenance expenses in the future. The emergency generator serves the condenser water loop cooling towers and pumps. In the event of a power outage, the walk-in coolers and freezers won’t defrost.
Four of the resort’s 35 electrical services were implemented to meet the needs of the hotel’s vast electrical load. To distribute power across such a vast area, the construction contractor relayed circuits for miles to provide the exterior lighting for the executive course and the two-acre putting green, along with auxiliary buildings, the retail village, hotel, performance center, etc. Following suit with the owner’s vision, the power distribution across the resort was kept underground so as not to distract from the resort’s luxurious aesthetics.
One major challenge for the electrical team was to provide sturdy, underground pathways for the electrical wiring that could maintain the integrity of the electrical connections despite the fact that the resort was constructed on expansive clay. Varying moisture levels in the soil will cause the clay to rise and fall with the seasons. Geotechnical reports have indicated that the ground could variate as much as 12 inches over the course of a year.
The electrical team designed a wire casing with flexible joints that protects the underground electrical distribution while allowing it to ebb and flow with the expansive clay. The underfloor sanitary distribution also ebbs and flows with the building. The system is “hanging” to the building via a set of plumbing hangers that were cast into the building’s subfloor. This allowed the sanitary piping to move with the building as the absorbent clay released and absorbed moisture throughout the year.
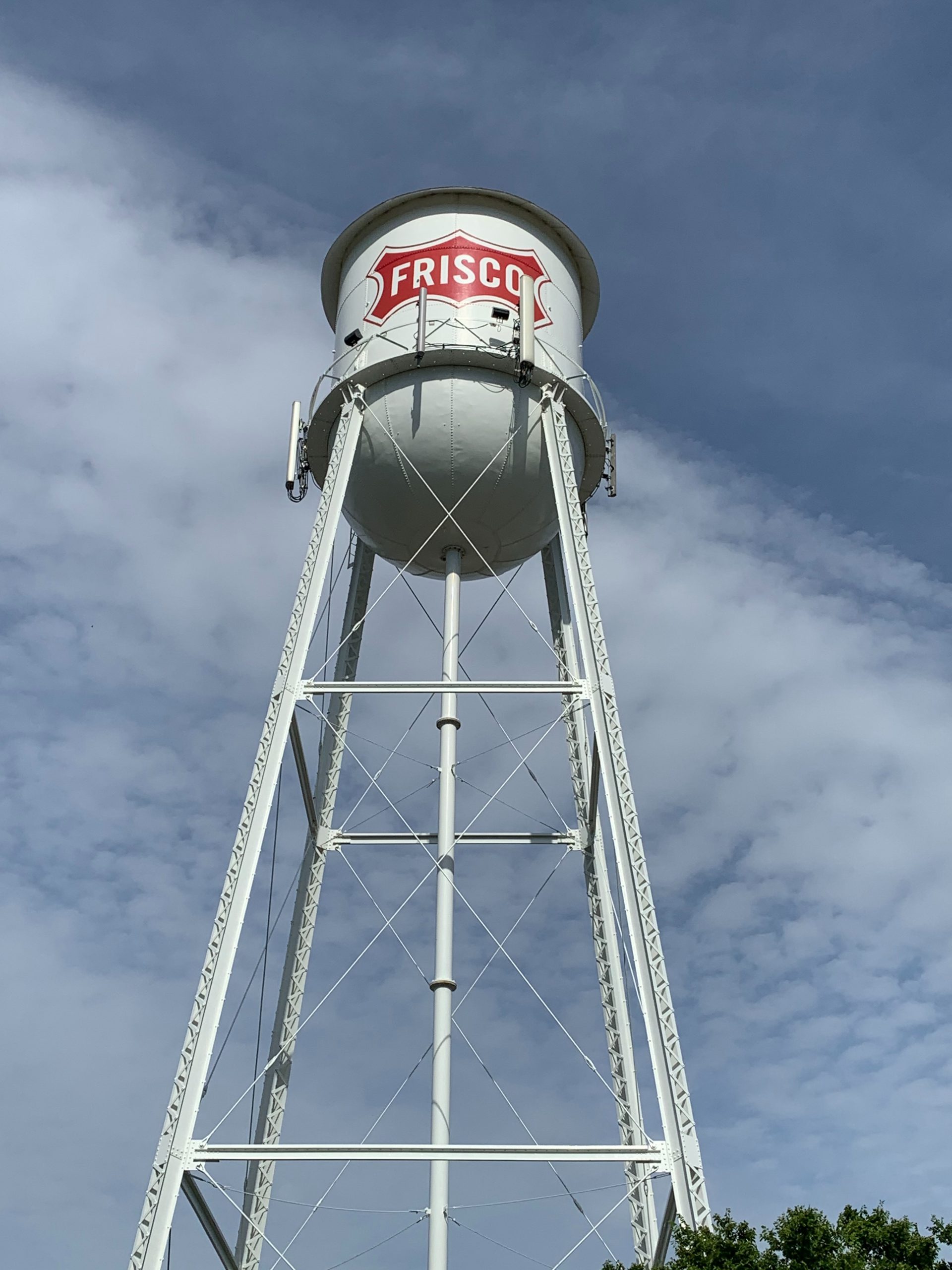
Felt, Not Seen
The sprawling hotel is the centerpiece of the resort campus. It sets the tone for a guest’s experience with grandiose floor-to-ceiling windows overlooking 450 acres of championship-caliber golf courses.
Accents of walnut and limestone adorn the walls, pillars, and ceilings of the open-concept hotel with carpets that take inspiration from traditional golf-attire pinstripes and contemporary farmhouse lighting fixtures, a nod to the style’s popularity amongst Frisco residents and the agrarian-rooted identity of the Dallas suburb. The natural hues and warm beige tones allow the structure to feel impressive yet approachable. Our mechanical and electrical teams pioneered a slew of unconventional accommodations to adequately supply the space with ample power and climate control components without detracting from the lobby’s extravagant “wow” factor.
“The goal was to be felt, but not seen,” Justin Olson explained. Justin Olson is an Alvine Associate Principal who was the lead electrical engineer on the project. “With all of the different ornate sculptures, design work, and overall aesthetics, we aimed to provide something that delivered on what the client needed without taking away from the exemplary work of the interior designer.”
Justin’s experience was crucial due to the project’s ambitious goals and unique nature.
“Ensuring the life safety components of the project were the best they could be was always at the top of our list of priorities,” Justin concluded.
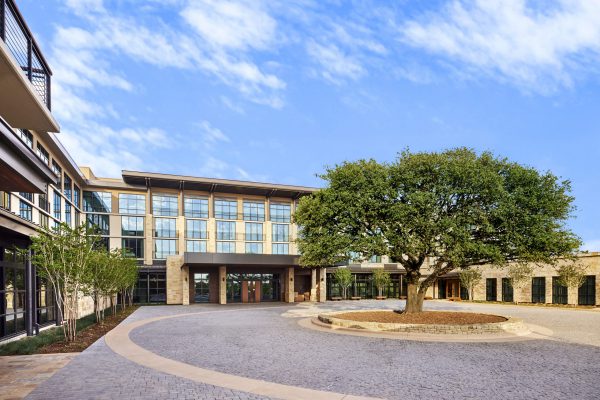
A Tight Squeeze
One of the biggest challenges with providing MEP services for one of the most luxurious golf resorts in the country was bringing robust electrical and mechanical capabilities that cater to a customized hotel guest experience (personal climate control, à la carte style amenities such as poolside cabana access, in-room energy management, etc.). Maximizing guest space for a hotel of this scale is crucial for a client’s ability to bolster their earning potential. Something as minuscule as two feet of space saved in a guest room layout can equate to over 1,000 square feet of extra space to utilize in the facility. One of the first areas a hotel looks at to save on space is the MEP component housing. Alvine’s electrical and mechanical teams had to craft unique layout solutions to meet the hotel’s tight spacing requirements.
“The goal of hotel design is to find space layouts that maximize the number of rooms the structure can hold without compromising the guest experience,” Tjaden explained. Tjaden is the lead mechanical engineer on the Omni Frisco project and has over seven years of experience. “All the guest rooms are covered using a chilled water loop system, and each has its own vertical fan coil, which required creativity to integrate since the hotel wanted low floor-to-floor heights to maximize space.”
A resort of this scale required three 550-ton water chillers with a chilled water loop dedicated to the hotel facility. In order to be consistent with the hotel’s infrastructure theme of “felt, but not seen,” three-inch water lines surrounded by an inch of insulation supply in-room vertical fan coils. However, despite this space-saving technique, there was still little room for electrical integration, telecom wiring, and fire protection water supply pipes.
Space was so tight in the hotel guestrooms that no MEP systems could be routed below the slab in the guestrooms. The project team decided to paint the bottom of the concrete slabs to utilize them as the guestroom ceilings. The design team resolved challenging limited space requirements by using the perimeter soffits to route fire protection piping, saving room for MEP integration in the suites.
The lobby also utilizes 18-foot floor-to-floor heights, offering extra space for the mechanical team to run vertical chilled water pipes behind the fan coils— a technique that allowed the mechanical crew to take ample advantage of the lobby’s extra ceiling space.
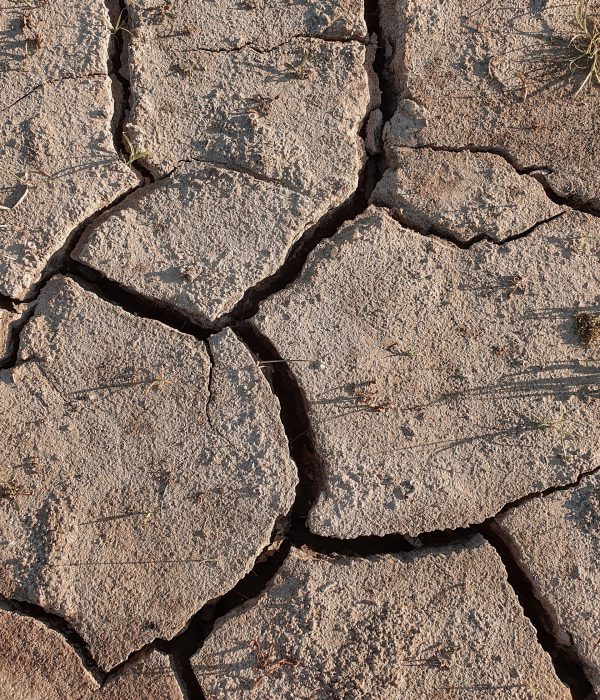
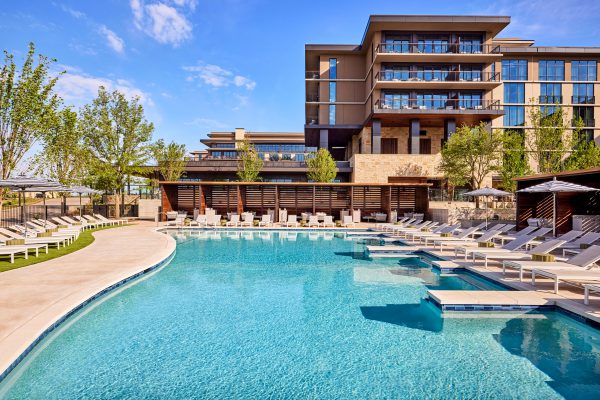
Staying the Course
While the client initially signed Alvine on through the design development phase, they ultimately concluded that our staff’s knowledge from the previous phases made us the best choice for the construction administration phase. Coordinating construction with the numerous contractors needed to bring a project of this scale to life is a testament to the Alvine reputation and unique competency within construction administration.
The unique nature of the project caused the client to reimagine and rethink certain areas as construction commenced. Meeting the demand of these changes required our team to spend extensive time planning with the interior designer as well as coordinating extensive collaboration with the owner to meet demands while staying on time. The project had a hard deadline date and needed to be ready and waiting for the upcoming PGA season.
When the owner initiated changes throughout construction administration, the design team worked diligently to quickly update design documents as the construction team was on the clock. Direct collaboration with all the facility contractors allowed the design team to update them on upcoming changes so they could rethink their workflows and project management strategies.
“We were able to integrate the changes quickly thanks to our enhanced level of knowledge of the project and experience and ability to coordinate as a team,” Justin Olson concluded. “Our team culture has allowed us to come up with all-encompassing, innovative solutions on short turnarounds.”
Learn more about the team behind Omni PGA Frisco.
Images Courtesy of Omni PGA Frisco Resort